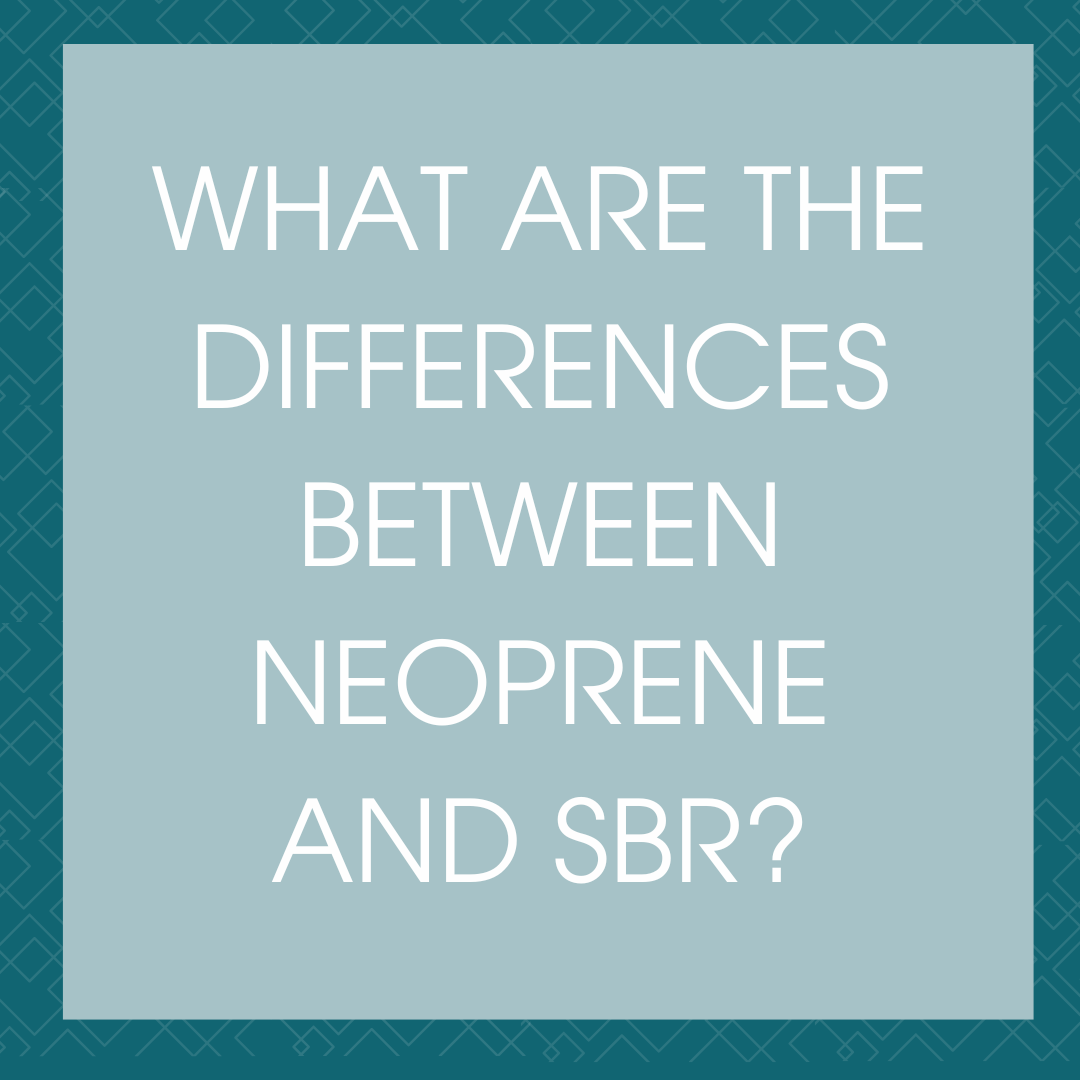
Neoprene vs SBR Rubber: Understanding the Differences
Share
When it comes to rubber materials, two of the most commonly used types in industrial, automotive, and recreational products are Neoprene and SBR (Styrene-Butadiene Rubber). While both are synthetic rubbers, they have distinct characteristics that make them better suited for different applications.
In this blog, we'll take a deeper dive into the differences between Neoprene and SBR, from their properties to their uses, and help you understand which rubber might be best for your needs.
What is Neoprene?
Neoprene, (also known as Polychloroprene), is a synthetic rubber developed by DuPont in the 1930s. It is made from the polymeriSation of chloroprene, a chemical compound, and has a wide range of applications due to its flexibility and resistance to various environmental factors.
Key Properties of Neoprene:
- Chemical Resistance: Neoprene is known for its resistance to oils, solvents, fuels, and other chemicals, making it ideal for use in automotive and industrial seals, gaskets, and hoses.
- Weather and UV Resistance: It holds up well against exposure to the elements, including sunlight, ozone, and oxidation, which makes it a popular choice for outdoor products and marine environments.
- Temperature Resistance: Neoprene has a good balance of flexibility and heat resistance, performing well in temperatures ranging from -40°F to 250°F (-40°C to 121°C).
- Good Physical Strength: It has strong abrasion resistance, elasticity, and impact resistance, making it durable and long-lasting.
Common Applications of Neoprene:
-
Wetsuits: Neoprene is commonly used in the production of wetsuits, due to its ability to provide thermal insulation and flexibility in water environments
-
Automotive Parts: It is widely used in gaskets, seals, and hoses that need to withstand harsh chemicals and high temperatures.
-
Protective Gear: Neoprene is also used for knee pads, elbow pads, and other protective gear, offering cushioning and support.
What is SBR Rubber?
SBR, (or Styrene-Butadiene Rubber) is another type of synthetic rubber, produced by the copolymerisation of styrene and butadiene. It was first developed in the 1920s as a more cost-effective alternative to natural rubber.
Key Properties of SBR:
- Cost-Effectiveness:One of the main advantages of SBR is that it is relatively inexpensive to produce, making it a preferred choice for large-scale manufacturing.
- Wear Resistance: SBR is known for its durability, especially in terms of abrasion resistance. It performs well in dry conditions but tends to degrade when exposed to oils, fuels, and chemicals.
- Temperature Resistance: While SBR can handle a reasonable range of temperatures (typically -40°F to 180°F / -40°C to 82°C), it doesn't fare as well as Neoprene in extreme conditions.
- Lower Chemical Resistance: SBR is less resistant to oils and solvents compared to Neoprene, which limits its applications in industries where such exposures are frequent.
Common Applications of SBR:
- Tires: The majority of car tires are made with SBR, as it provides excellent wear resistance and good performance on dry and wet roads.
- Footwear and Industrial Products: SBR is often used in the production of rubber soles, gaskets, and seals, where cost is a primary factor, and chemical resistance isn't as critical.
- Conveyor Belts: It is also used in manufacturing conveyor belts, where abrasion resistance is key.
Comparing Neoprene and SBR: Key Differences
Now that we’ve covered the basic properties and uses of Neoprene and SBR, let's dive into their key differences:
Which One Should You Choose?
The choice between Neoprene and SBR will largely depend on the specific requirements of your application.
-If you need chemical resistance, weather durability, and high-performance in a variety of environments, Neoprene is the better choice. It's ideal for applications like wetsuits, automotive gaskets, and seals that are exposed to a range of elements and chemicals.
- If cost is a primary factor and the application does not require significant exposure to oils, fuels, or extreme weather, then SBR may be the right option. It is particularly well-suited for applications like tires, footwear, and conveyor belts, where wear resistance and cost-effectiveness are the main considerations.
Conclusion
Both Neoprene and SBR are essential materials in the rubber industry, but they offer different advantages. Neoprene excels in applications requiring chemical and weather resistance, while SBR stands out for its cost-effectiveness and wear resistance in dry conditions. By understanding their unique properties and performance characteristics, you can make an informed decision about which rubber is best suited for your needs.
Let us know if you’ve got a specific project in mind—choosing the right material is key to ensuring durability and long-term performance!